How to audit physical assets inventory
SageData is based in Ottawa, Ontario, Canada
Introduction
An inventory check, or audit, of physical assets can be a challenging and time consuming endeavor. For many years
SageData have been providing inventory management solutions that make the auditing a simple, fast and accurate process. Learn how
a combination of our BassetPro software, barcode technology and mobile computers make this happen. For the purpose of this
explanation, we will assume: that all equipment has been received and entered into the system; that all locations have been set
up (could be cubicle, office, shelf, store-room), and that all users of the MUs (Mobile Units) have been given username and
password.
There are two activities: data collection, and reporting.
Data Collection
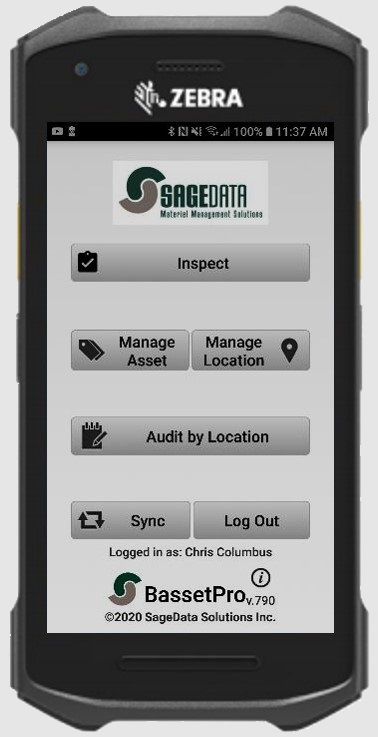
The objective is to make the data collection easy, fast and accurate.
The user logs on to the MU, places it in its docking station, and initiates a synch. This moves the most recent information from
BassetPro to the MU. Plenty of capacity. Can accommodate a million assets, if required.
User goes to first location, scans the barcoded location ID tag. The MU displays the location. User then scans the barcoded asset
tag on each asset. The MU displays information related to each asset as it is scanned. So if there are ten assets at that
location, the user pulls the trigger eleven times. No keyboard entry. User moves to the next location, and repeats the process.
So this is very fast, two or three seconds per asset. Time to perform the inventory is determined mainly by the time to walk
between assets. Training time for this might be five minutes, so not limited to a few skilled people.
Process is repeated until all locations have been covered. No restrictions. Items can be scanned many times (if you are not sure, scan it again). And, of course, help is provided for items without a tag, or in the wrong location. And this can be extended to tracking who is responsible for each asset, as well as where assets are. That is it. Audit is done. Information is in the MU. For clients who are not limited by security concerns, information can be moved back to BassetPro using Wi-Fi or mobile network. For high-security clients, user returns to the workstation, drops the MU in the docking station and initiates a transfer. In that transfer, data is moved from the MU to the workstation, merged with data that has previously been received from other MU, and passes the latest data set back to the MU. So all ready for the next audit. And of course, the MU can also be used to record the movement of items from one location to another.
Reporting
The system provides a wide range of reports. These can include a listing of all assets in a specific location, or
across all locations. It can filter by any field, only showing equipment from a particular manufacturer, or model number. It can
show the history of a particular item, from first receipt through deployment, movement, repair, inventory check, and eventual
disposal. It can show all activities in a given time period, such as items checked, or moved or disposed or received last month
or any other month or any other period. Many clients use the system for asset life-cycling, providing reports, for instance, on
all monitors more than three years old.
Some clients use the system for enhanced security, ensuring that all secure equipment is in safe storage when required, and also
checking who was the recipient when secure hardware is issued on short-term allocation. And all these reports are available on
screen, printable, or in pdf format, useful for forwarding to other interested parties.
The reporting can be restricted, or other users can be given access, either full access (to add, edit or dispose items) or
restricted access - see the data but don’t change it.
We would be happy to help with your inventory auditing needs.
Follow these links for more information on:
- Fixed assets management
- Warehouse management system
- Fire equipment inspection
QAOK4365