Inspection Systems for Safety, Availability and Maintenance
SageData is based in Ottawa, Ontario, Canada
Inspections are required for many reasons. A simple inventory check. A
safety check. A check to determine what maintenance action is required. These inspections
usually involve a visit to the item to be inspected, and sometimes an inspection against
a checklist. So the issues include: guidance to the inspector on where to go, how to
identify the equipment or location to be inspected, and how to efficiently capture the
information required.
This article explains how barcode technology, NFC (Near Field Communication) and
passive RFID can be used to improve the inspection process, to make it easy, fast and
comprehensive.
Safety checks can apply to food, fire extinguishers, weapons, SCBA (Self Contained
Breathing Apparatus) and HVAC equipment. Maintenance checks are required to ensure the availability of
equipment (especially standby emergency equipment) when required.
Inspection systems are another strength of SageData. We helped multiple clients to make their inspection business time efficient, accurate and reliable.
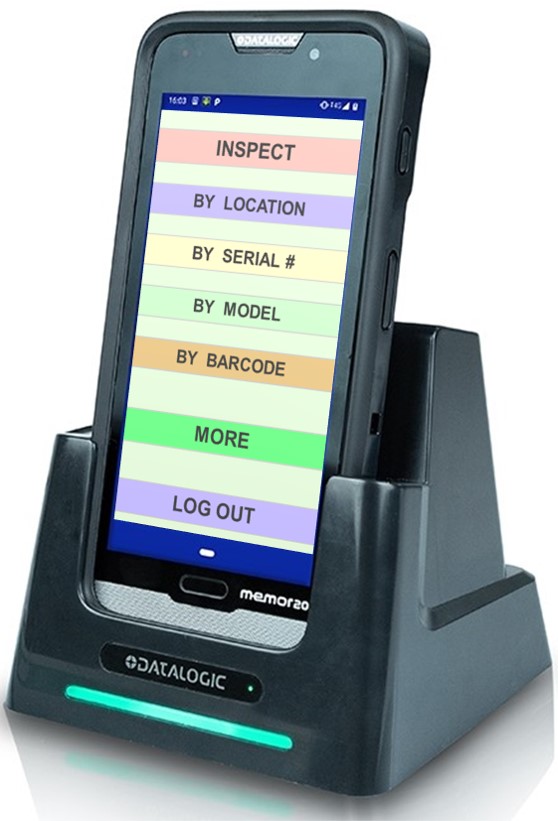
For example, an important task of inspecting fire extinguishers. This task has to be done at the location of the fire extinguisher. An inspector would travel to the site where the equipment to be inspected is located, find the equipment, have a look at it, and take notes. These notes will likely form a report that the inspector needs to produce.
Now, armed with the SageData mobile information collector, the inspector will only need to log into the information collector, choose an inspection site and follow the on-screen directions to the closest fire extinguisher. At the location the inspector scans the barcode, prompting the fire extinguisher information to appear on the screen, updates relevant fields, and saves the information. The information collector will now guide the inspector to the next object of inspection.
The SageData solution saves time and enables an inspector unfamiliar with the building layout to find all the fire extinguishers and accomplish tasks efficiently without wandering around looking for a specific location. The inspection report is automatically generated as the inspector moves from one object of inspection to another. The building manager has access to information that shows which units were inspected, who inspected them, and when they were inspected. In some special cases, such as inspection of fall prevention equipment, the system verifies that the inspector has the appropriate qualifications.
Inspector in practice merely indicates with one click that the equipment is fit for service. If a new inspector is presented with unusual equipment, the system can prompt with a checklist. If the equipment is rated as not fit for service, the system can present a list of the most likely failure reasons, with the option to add an appropriate note.

While the example of fire extinguishers' inspection covers only one case, the SageData solution can be used for inspection of any physical item. For example, it can be used to log the conditions of art work or the results of power equipment (e.g., portable power generator) inspection.
We will be happy to discuss your business needs and recommend a suitable solution.
If you found this useful, you might also want to review:
- an introduction
to barcode technology
- an introduction to RFID
- occupational health
and safety inspection
- consulting
services: barcodes and their applications
QAOK5026