Construction Equipment:
Manage it, Track it
Easily, Quickly Accurately
SageData is based in Ottawa, Ontario, Canada
Background
A client operated a construction business, and owned a wide variety of equipment, from chain-saws to graders. Much of this was worth hundreds of thousands of dollars, and by its very nature, was frequently moved from location to location, and often left unattended in remote locations overnight. Equipment was stored at several depots, and from time to time equipment was moved to the wrong location. The insurance company had mandated live tracking for the most expensive equipment, but this required wireless connection through the mobile cellular network, and that in turn generated a monthly bill for each item to be tracked. The cost was adding up.
The final straw
that led to an implementation of SageData's solution was the
loss of some
critical
equipment.
It had been returned to the wrong depot, and stored with other equipment. Much time
was spent searching for it, and the rental of substitute equipment cost money and time. When
eventually,
the equipment was discovered, by accident, the justification was made for a tracking
system that covered items beyond the top tier mandated by the insurance company.
The solution
The most expensive equipment
Items above $250,000 were already being tracked by a real time system. Monthly costs
were
too
high to extend this over the rest of the fleet, so an alternative strategy was
developed for items between $20k and $250k. These items would be fitted with an active RFID tag.
A
mobile receiver would be installed in one or more of the supervisors vehicles.
Whenever any of
these vehicles came within a hundred metres of any tagged equipment, its location would be
recorded.
No
action was required of the driver, the system was totally passive. Whenever the vehicle
returned to any of several depots, the information would be passed to the main server, and made
available to all authorized personnel.
This system operates passively, and provides the last known location of the equipment to an
accuracy of
100 metres. There is no longer any question of which equipment is in which depot. Fixed
monitors constantly monitor the stored equipment, and record the exact time of its removal or
return.
Less expensive equipment
For items to $20k, two solutions was proposed. For simple equipment, such as chain
saws,
the
barcode provides an effective solution. Items can easily be tagged, and a handheld
portable reader, or reader directly attached to a desktop computer, can be used for audit
purposes
and
to track maintenance activities.
For the equipment that gets dirty, such as water pumps, an HF RFID tag can be used. This is
easy to
read, even when covered in mud, and is smaller and less expensive than the active tags used
on the more expensive equipment.
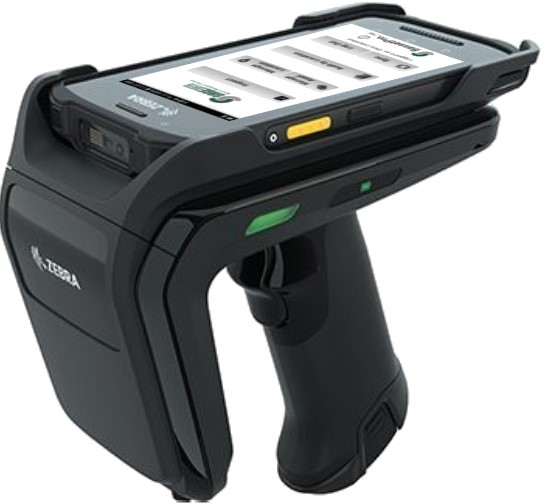
Return on Investment
Knowledge of the exact
location of each equipment saves time and money, particularly when equipment is needed on
short notice. Avoiding lost
equipment avoids lost
time on projects, saving overall
costs and
helping
to avoid penalty clauses. When the location and status of each item is known,
duplication of equipment can be reduced, saving capital costs.
When the system is used to
track
maintenance tasks, wear and tear can be reduced, and equipment life can be extended. The cost of
the RFID tags, the RFID tag readers, and the RFID management software can quickly be recouped.
Summary
Both barcode and RFID systems provide better control and reduced costs of
operation. Implementation of these technologies means that equipment can be tracked and managed
easily, quickly,
accurately.
If you would like to know more about these technologies,
please feel free to contact us.
If you found this useful, you might also want to review:
-
managing landfill with barcode technology
- an introduction to RFID
- RFID in a warehouse - a brief video
-
active RFID tags
QAOK4356