The Application of RFID in Manufacturing
SageData is based in Ottawa, Ontario, Canada
Introduction
An explanation of how using RFID technology in Manufacturing operations can
save time, reduce costs and improve quality.
We recommend that you first read Barcodes for
Manufacturing
since many of the Auto-ID principles discussed for barcodes also
apply
to
Radio Frequency Identification.
Application of RFID Tags
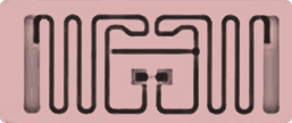
As with barcodes, RFID tags can be used to identify a variety of items as they move through the manufacturing process. Two of the strengths of RFID technology are the ability to read multiple tags in one pass, and to read tags that are not within line of sight (for example, inside a cardboard box).
If not used carefully, these strengths can also become weaknesses in the
manufacturing process because of mis-reads. Often, however, RFID labels also carry a
barcode. We advocate using the best fit
technology depending on circumstances. If you
need to record an individual item passing a manufacturing station, and there are many
RFID-tagged items in the vicinity that may be read at the same time, then scanning the
barcode makes sense.
The ability for RFID readers to increase and reduce their power effectively changes the read range. When used intelligently by software, this variable read range capability can be very powerful.
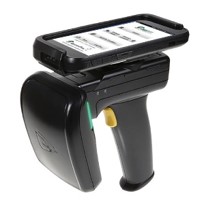
As with barcodes, beyond item identification, RFID tags can also identify individual operators (so that a record is kept of who did what) and location information, which can be used to identify and eliminate bottlenecks, eliminate delays due to out of stock situations, and improve quality.
Managing inventory with RFID
When designed well, inventory management with RFID is a breeze. If the manufactured items are individually identified (for example, a shelf full of computers), and locations are carefully labelled, then a simple button push can inventory and timestamp tens or hundreds of items in one pass.
For SKU-based inventory (for example, low-value items such as screws, washers, nuts) then RFID can be applied in a couple of ways. If it is convenient and cost-effective to individually identify aggregated quantities of stock (for example, 100 nuts, bolts and washers in a kit for sale or internal use), then the same principles as for individually identified items can be used. If a more conventional stores model is used, RFID tags can still be used or barcodes may be better - much depends on circumstances.
The same tools are used for put-away and picking, to maintain a moving inventory count. An MSL (minimum stock level) feature in the software helps ensure that stock is replenished in a timely fashion, avoiding disruption associated with shortage of raw materials.
Managing WIP (Work in Process)
By attaching a RFID tag to each item or each batch, progress through the manufacturing process can be recorded and subsequently analyzed. Reading of the tags can be completely automated with a reader at each station recording time in. When items have to be prioritized, they can be easily located either with fixed or mobile RFID readers.
Regulatory Compliance
In many processes there is a step which must be tracked and recorded. Perhaps a calibration, a sealing process, an inspection, or confirmation that a specific test has been conducted. The use of RFID or barcode technology facilitates the collection and management of certification
Traceability
In some industries, particularly food or aerospace, there is a requirement for traceability. AutoID technology such as RFID or bar codes enable materials to be tracked from receipt to shipping. One of our clients tracks every component for an aeronautical application from receipt to shipment. In a system with several thousand components, the date of receipt and lot number of every item can readily be identified.
Conclusion
RFID technology enables large amounts of data to be collected without adding to the overhead of manufacturing tasks, and often without human effort. Immediate benefits include the reduction of paperwork, and the timely dissemination of information related to manufacturing. Although there are considerable savings in reduced time required for routine operations, the biggest benefit is the reduction of time wasted dealing with unplanned disruption due to misplaced WIP or shortage of raw materials.
Contact us for more information.
If you found this useful, you might also want to review:
-
an introduction to barcode technology
- an introduction to RFID
- mobile data collectors
-
consulting
services: barcodes and their applications
QAOK4355