SageData solutions for Manufacturing and Retail
SageData is based in Ottawa, Ontario, Canada
Introduction
Manufacturing process is a fine tuned process that requires a lot of attention to mitigation of potential bottlenecks. The bottlenecks could be of various kinds but they all contribute to headaches in manufacturing. Inventory management is one of the sensitive areas for the manufacturers that may become a real headache if not managed properly.
The Challenge
Companies that receive orders for their products, manufacture and ship merchandise need to watch for potential shortages of components that make the final product.
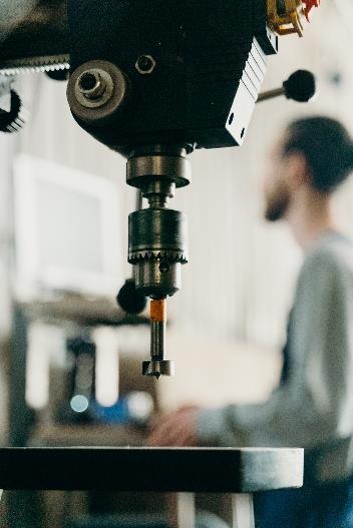
How to ensure that the sales team is aware how many items can be ordered at any point? What
happens
if there are multiple sales agents and or an on-line ordering system in addition?
Some companies also permit the sales agents to reserve some products based on an expectation of
an
order. This further complicates the inventory management process as the components needed to
assemble a product must be subtracted from the existing inventory. There could be a situation
when a
number of orders compete for the same stock of components potentially causing confusion among
the
manufacturing staff. They may literally see a pile of the required components sitting on the
shelf
while their mobile data collectors show zero inventory available.
This leads to a question on how to address this and other complexities of the manufacturing
process.
The Solution
SageData Solutions helped multiple clients to implement a system that efficiently tracks pending orders, inventory levels of various components, orders in process of manufacturing and much more. Our flagship software solution BassetPro in combination with Barcode and RFID technologies addresses the manufacturing inventory management challenges.
BassetPro has the capability to integrate with the back end systems like SAP, Quickbooks,
etc.
BassetPro exchanges information with the back end system so a new or an existing order is
instantaneously reflected in the components / materials inventory count. Likewise, the
components
taken from the inventory for an order manufacturing process are automatically subtracted from
the
inventory. This information is reported to the back end system and reflected in the product
availability used by the sales team and or an on-line ordering system. We adjust our software to
match the existing client's processes ensuring a smooth integration process.
BassetPro solution provides a number of specific reports allowing a real-time managerial
supervision
on the component inventories and associated activities.
Similarly, our solution provides retail clients with an ability to efficiently track in real
time
the merchandise from the moment of its arrival to the moment it leaves the store or a warehouse,
know the stock levels, pending and received orders, and much more.
BassetPro has been in the field for over 25 years. Our solution underwent multiple revisions and acquired new capabilities making it a very flexible mobile software platform.
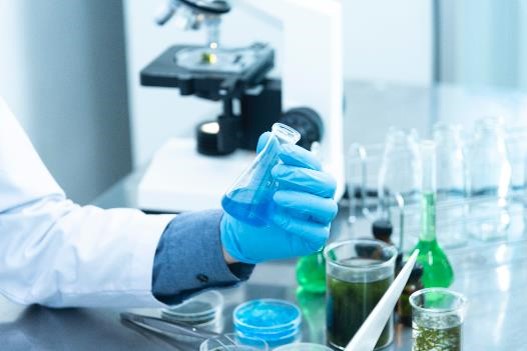
For more information consider browsing the following links:
- an introduction
to
asset
management
- barcode technology for
manufacturing
- occupational health
and
safety inspection
- chemical
inventory
management
- small warehouse
management
QAOK4367